When your goal is to stop tampering before it starts, nothing works better than a fragile sticker. These ultra-thin labels tear into countless pieces the instant someone tries to peel them away, leaving behind unmistakable proof of interference. The guide below walks you through every decision point you need to master when selecting fragile paper for your next security project.
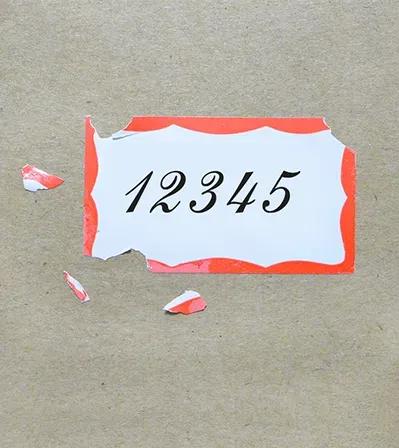
1. Understand the Core Material
Fragile paper is engineered to be brittle. Typical basis weights range from 50 to 80 gsm, yet the sheet’s internal fibrillation is deliberately low. The result is a fragile sticker that shatters like thin glass when flexed or lifted. Ask your supplier for tensile-strength data—anything above 15 N/15 mm is too strong to meet true destructibility standards.
2. Security Level Checklist
A decorative label is not a security label. Verify these three features:
Hidden VOID pattern that blossoms across the surface when the fragile sticker is removed.
Micro-text smaller than 0.3 mm that fractures into illegible fragments.
Solvent-reactive ink that blurs upon contact with alcohol or acetone.
If the supplier cannot demonstrate all three, keep searching.
3. Match the Adhesive to the Job
The adhesive is half the security story.
Permanent acrylic: ideal for glass vials, PVC blister packs, and powder-coated metal enclosures.
Freezer-grade rubber: maintains tack down to 40 °C for pharmaceutical cold-chain applications.
Oil-resistant acrylic: survives cutting fluids on machined parts.
Run a 24-hour peel test on every substrate. A proper fragile sticker should transfer 100 % of its fiber to the surface when removed, leaving no clean backing behind.
4.Surface Compatibility Matrix
Glass: requires high-coat-weight adhesive to prevent edge lift.
Cardboard: needs a primer to stop fiber tear-out.
Stainless steel: benefits from a slightly thicker adhesive layer to fill micro-scratches.
ZOLO’s lab will send you a complimentary adhesion report within 48 hours—simply mail a 10 cm × 10 cm sample of your target surface.
5.Print Method & Durability
Fragile paper accepts flexo, digital, and thermal-transfer printing.
Flexo: speeds up to 300 m/min with 80 gsm face stock.
Digital: perfect for serialized barcodes or variable QR codes on 60 gsm sheet.
Thermal-transfer: produces crisp resin-ribbon images resistant to smearing.
For outdoor exposure, add a UV-blocking varnish; it extends fade resistance to 90 days without compromising destructibility.
6.Size, Shape & Customization
Standard dies include circles from 8 mm up to 50 mm, rectangles, and oval shapes. Need a custom outline? ZOLO’s laser die table creates a unique fragile sticker silhouette in under 48 hours. Back-slits (2 mm) enable auto-dispensing, while sequential numbering or NFC embedding can be added without extra tooling.
7.Environmental & Compliance Factors
REACH & RoHS compliant inks and adhesives.
FDA 21 CFR direct-contact approval for food and pharmaceutical labels.
·30 % post-consumer fiber option.
Each order ships with a Certificate of Analysis and an SGS lab report.
8.Cost vs. Volume Reality Check
Thanks to ZOLO’s 400,000 m² monthly capacity, minimum orders start at only 1,000 labels. Unit prices drop below $0.01 when volumes exceed 100,000 pieces. Whether you need rolls, fan-fold stacks, or individual sheets, the format change is free—no hidden tooling fees.
9.Rapid Prototyping & Global Delivery
Upload artwork by 5 p.m. Shenzhen time and receive a digital proof by 9 a.m. the next day. Free DHL samples land in North America or Europe within 72 hours. Full production ships in five working days, sea freight to Rotterdam in 26 days, air freight anywhere in three.
10. Final Action Plan
Print this checklist, tick every box, and you will never again wonder how to choose fragile paper for a fragile sticker. The right combination of thin destructible face stock, matched adhesive, security print, and compliance documentation turns every label into a low-cost, high-impact tamper-proof seal that protects your brand and your customers.
When your goal is to stop tampering before it starts, nothing works better than a fragile sticker. These ultra-thin labels tear into countless pieces the instant someone tries to peel them away, leaving behind unmistakable proof of interference. The guide below walks you through every decision point you need to master when selecting fragile paper for your next security project.
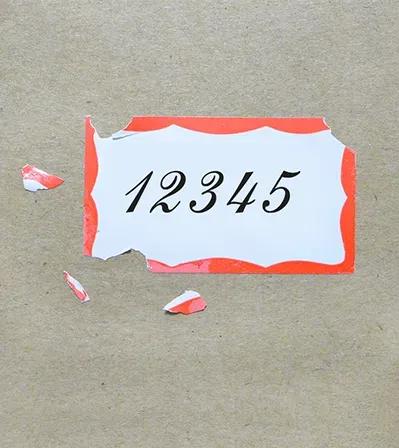
1. Understand the Core Material
Fragile paper is engineered to be brittle. Typical basis weights range from 50 to 80 gsm, yet the sheet’s internal fibrillation is deliberately low. The result is a fragile sticker that shatters like thin glass when flexed or lifted. Ask your supplier for tensile-strength data—anything above 15 N/15 mm is too strong to meet true destructibility standards.
2. Security Level Checklist
A decorative label is not a security label. Verify these three features:
Hidden VOID pattern that blossoms across the surface when the fragile sticker is removed.
Micro-text smaller than 0.3 mm that fractures into illegible fragments.
Solvent-reactive ink that blurs upon contact with alcohol or acetone.
If the supplier cannot demonstrate all three, keep searching.
3. Match the Adhesive to the Job
The adhesive is half the security story.
Permanent acrylic: ideal for glass vials, PVC blister packs, and powder-coated metal enclosures.
Freezer-grade rubber: maintains tack down to 40 °C for pharmaceutical cold-chain applications.
Oil-resistant acrylic: survives cutting fluids on machined parts.
Run a 24-hour peel test on every substrate. A proper fragile sticker should transfer 100 % of its fiber to the surface when removed, leaving no clean backing behind.
4.Surface Compatibility Matrix
Glass: requires high-coat-weight adhesive to prevent edge lift.
Cardboard: needs a primer to stop fiber tear-out.
Stainless steel: benefits from a slightly thicker adhesive layer to fill micro-scratches.
ZOLO’s lab will send you a complimentary adhesion report within 48 hours—simply mail a 10 cm × 10 cm sample of your target surface.
5.Print Method & Durability
Fragile paper accepts flexo, digital, and thermal-transfer printing.
Flexo: speeds up to 300 m/min with 80 gsm face stock.
Digital: perfect for serialized barcodes or variable QR codes on 60 gsm sheet.
Thermal-transfer: produces crisp resin-ribbon images resistant to smearing.
For outdoor exposure, add a UV-blocking varnish; it extends fade resistance to 90 days without compromising destructibility.
6.Size, Shape & Customization
Standard dies include circles from 8 mm up to 50 mm, rectangles, and oval shapes. Need a custom outline? ZOLO’s laser die table creates a unique fragile sticker silhouette in under 48 hours. Back-slits (2 mm) enable auto-dispensing, while sequential numbering or NFC embedding can be added without extra tooling.
7.Environmental & Compliance Factors
REACH & RoHS compliant inks and adhesives.
FDA 21 CFR direct-contact approval for food and pharmaceutical labels.
·30 % post-consumer fiber option.
Each order ships with a Certificate of Analysis and an SGS lab report.
8.Cost vs. Volume Reality Check
Thanks to ZOLO’s 400,000 m² monthly capacity, minimum orders start at only 1,000 labels. Unit prices drop below $0.01 when volumes exceed 100,000 pieces. Whether you need rolls, fan-fold stacks, or individual sheets, the format change is free—no hidden tooling fees.
9.Rapid Prototyping & Global Delivery
Upload artwork by 5 p.m. Shenzhen time and receive a digital proof by 9 a.m. the next day. Free DHL samples land in North America or Europe within 72 hours. Full production ships in five working days, sea freight to Rotterdam in 26 days, air freight anywhere in three.
10. Final Action Plan
Print this checklist, tick every box, and you will never again wonder how to choose fragile paper for a fragile sticker. The right combination of thin destructible face stock, matched adhesive, security print, and compliance documentation turns every label into a low-cost, high-impact tamper-proof seal that protects your brand and your customers.